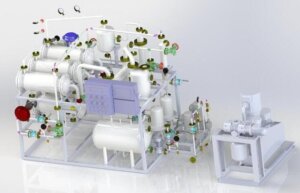
A Complete Guide: Membrane Separation Technology With Molecular Sieve Pervaporation Process
The principle of separation by PV process is to use the concentration difference or partial pressure difference of the components to be measured as the driving force for mass transfer, according to the dissolution performance of the raw material mixture in the membrane material, the diffusion rate and the difference in molecular size, so as to achieve the purpose of separating the components.
In this article, we will introduce the complete process and technology mainly about pervaporation membrane separation performance with inorganic molecular sieve membrane components.