Decolorizing Fish Oil: A Comprehensive Guide to Effective Purification
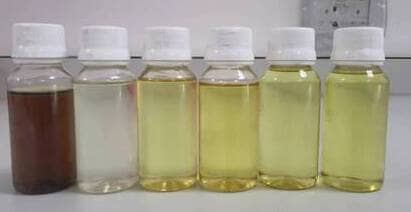
Fish lipids typically exhibit a range of colors when initially extracted and isolated as crude oil, such as yellow, brown, green, or even black, due to the presence of different types and quantities of pigments and particles.
To ensure appearance and quality, oil refineries generally need to refine the crude oil to remove the color and reduce these colorants.
The decolorization process is a critical step in the purification of fish oil esters, it helps to remove not only pigmented substances, but also remove trace metal elements in oil esters, phospholipids, saponification, odorous substances, residual pesticides, etc., which can contribute to off-flavors, rancidity, and reduced shelf life.
It is the last process before the oil is subjected to deodorization under high-temperature treatment for further removal of impurities.
By removing these impurities, the fish oil esters are given a clear and visually appealing appearance, enhancing their marketability and improving oxidative stability.
As a supplier of fish oil refining and purification equipment, we understand the requirements of omega-3 fish oil purification and the importance of decolorization in improving the quality and appeal of fish oil esters.
In this article, we aim to provide basic process information to help readers effectively select the decolorization process and equipment.
Efficient Adsorption Process for Heavy Metal Removal
Removal of toxic heavy metals from polluted water bodies is imperative for health and environmental protection.
To this end, chemical precipitation, chelate precipitation (flocculation), ion exchange, electrochemical, flotation, advanced oxidation, and membrane separation methods have been developed to address heavy metals, but no universal and effective treatment methods have been found so far.
The use of natural minerals to treat pollution and repair the environment is based on making full use of the laws of nature, reflecting the characteristics of natural self-purification.
The use of natural minerals to treat pollution and repair the environment is based on making full use of the laws of nature, reflecting the characteristics of natural self-purification.
Clay minerals have been used as excellent adsorbents due to the presence of different types of active sites on their surfaces, such as ion exchange sites, Lewis acid sites, and Bronsted sites.
The key to adsorption technology is the preparation of environmentally friendly, cheap, and efficient adsorbents.
Modified natural and synthetic clays such as kaolin, bentonite, montmorillonite, silver mica, and attapulgite are the most widely used clays for the preparation of high-performance nanocomposites.
This article mainly discusses advances in clay minerals and their derivatives for treating heavy metal effluent.
Effective Separation and Purification of Lactic Acid: Process and Equipment
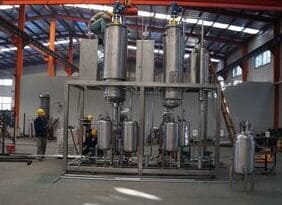
Understanding the crucial factors influencing lactic acid recovery, selecting appropriate separation and purification methods, and optimizing process parameters will contribute to higher yields, improved product quality, and increased efficiency. By unlocking the full potential of lactic acid separation and purification, businesses can benefit from enhanced productivity and meet the stringent demands of various industries.
Implementing these effective techniques and utilizing suitable equipment will not only streamline lactic acid production but also open doors to new opportunities and applications. Embrace the knowledge shared in this guide, and witness the transformative impact it can have on your lactic acid separation processes.
Fish Oil Winterization Process: Stabilizing Production with Effective Control Strategies
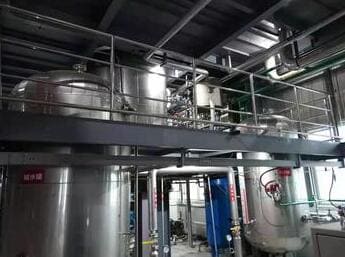
Different winterized fish oils can be produced by sequential treatment of incubation and filtering at increasingly decreased temperatures and controlling the temperature required for different freeze filtration. The lower the freezing point, the higher the unsaturated fatty acid content and the purer the quality of the winterized fish oil compared to normal refined fish oils.
The fish oil winterization and refining line can be optimized by optimizing the production process parameters on the equipment and control system, improving the professional skills and proficiency of the production operators, reducing the production cycle time per unit of product and promoting higher production efficiency, thus achieving an increase in the target capacity scale.
Supergravity Fractionation Machines: Revolutionizing Solvent Separation
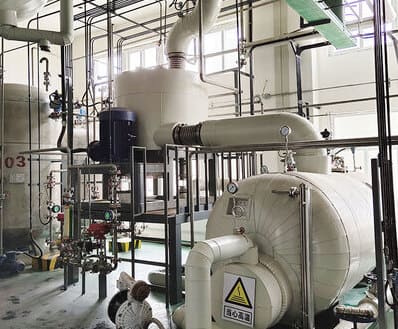
Supergravity distillation is a highly efficient technique for maximizing the effectiveness of distillation. Its wide range of applications in the petrochemical, pharmaceutical, biological and industrial sectors offers unparalleled advantages for the separation and purification of target substances.
Continuous or intermittent distillation recovery of organic solvents such as formaldehyde, toluene, methylal, ethylene glycol, acetonitrile, ethyl acetate, acetone, tetrahydrofuran, dimethyl sulfoxide, n-butanol, methylene chloride, silyl ether, cycloethane, isobutane, isopropanol, glacial acetic acid, acetic anhydride, DMF, DMSO, DMAA, DMDA, etc.
The Crucial Role of Hot Oil Transfer Pumps in Industrial Applications: Understanding Operations and Structures
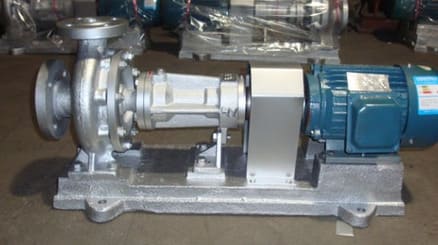
Hot oil transfer pumps play a critical role in numerous industrial applications where the efficient movement of heat transfer fluids is essential. These pumps are specifically designed to handle high temperatures and ensure the safe and reliable circulation of hot oil within industrial systems.
In this article, we will explore the importance of selecting the proper structure for hot oil transfer pumps, delve into their operational principles, and highlight key considerations when choosing the right pump for specific industrial applications.
How To Make Molecular Sieve Membrane: A Complete Guide
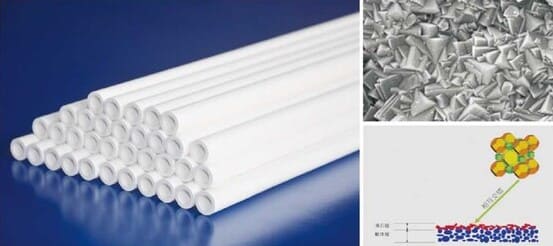
Molecular sieve membranes are a new type of porous inorganic material developed in the last decade by cross-linking molecular sieve grains.
Did you know that a molecular sieve membrane can separate molecules based on their size and shape? It is based on the dual principle of preferential adsorption and molecular sieving. The separation is achieved by selective adsorption, depending on the size or polarity of the molecules of the mixed system, through molecules of similar size but different polarity.
Today, molecular sieve membranes are commonly used in membrane permeation evaporation liquid separation, membrane-catalyzed reactions, separation of aromatic isomers, alkanes, and olefins, meteorological separation, separation of biochemical products, and environmental protection.
Let’s learn how to make a molecular sieve membrane with our detailed guide!
Our guide includes step-by-step instructions for the preparation, coating, and characterization of molecular sieve membranes, as well as the effects of different synthesis conditions.
A Complete Guide: Membrane Separation Technology With Molecular Sieve Pervaporation Process
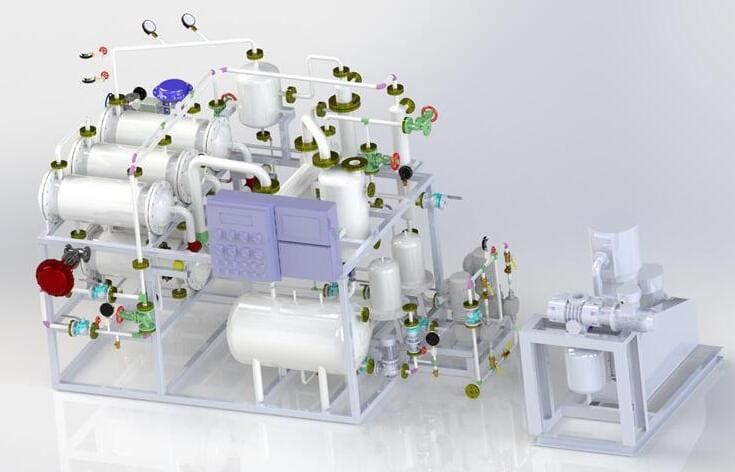
The principle of separation by PV process is to use the concentration difference or partial pressure difference of the components to be measured as the driving force for mass transfer, according to the dissolution performance of the raw material mixture in the membrane material, the diffusion rate and the difference in molecular size, so as to achieve the purpose of separating the components.
In this article, we will introduce the complete process and technology mainly about pervaporation membrane separation performance with inorganic molecular sieve membrane components.
Process Technology For Dehydration and Recovery of Ethyl Acetate
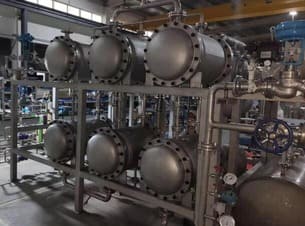
The increasing demand for ethyl acetate as an important raw material in various industries demands the need for advanced production processes and effective recovery and dehydration technologies.
The traditional production processes, although widely used, face challenges such as high energy consumption, low separation efficiency, and environmental pollution.
The pervaporation technique has emerged as a promising alternative due to its low energy consumption, no pollution, and good separation effect.
The optimization of the pervaporation process conditions can significantly improve its separation performance, making it a highly efficient and economic option for the recovery and dehydration of high-purity ethyl acetate on an industrial-scale production line.
The use of molecular sieve membranes in the pervaporation process has shown outstanding chemical stability and separation performance, making it a promising technology for the separation of ethyl acetate-water systems.
Methanol Recovery and Dehydration Process To Get 99.9%: A Complete Guide
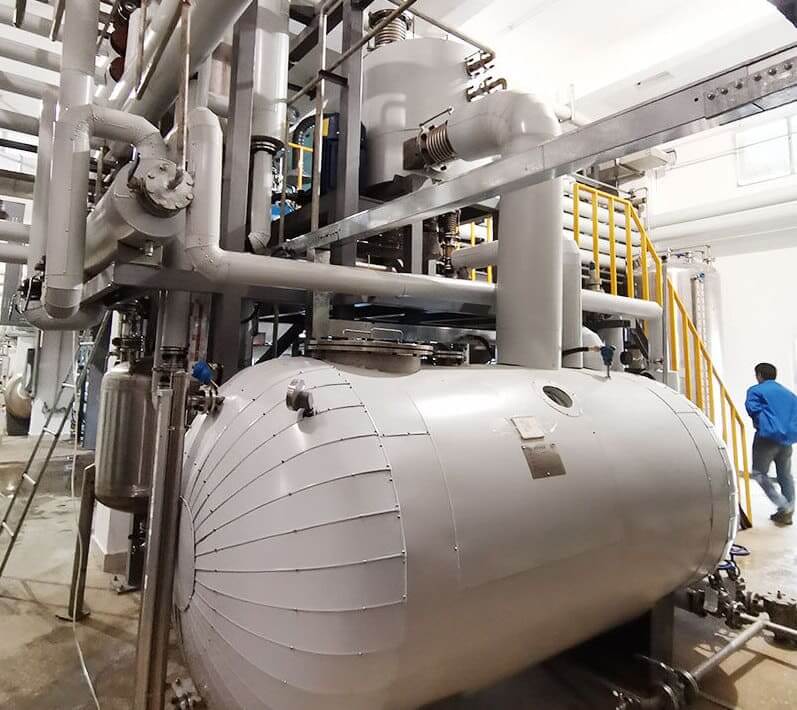
Methanol is an important chemical with a wide range of applications. With the advantages of high temperature stability, low volatility and excellent clean energy properties, it is widely used in the production of chemicals, solvents, fuels and fungicides.
Effective recovery and purification of methanol is essential for many industries, including the chemical, pharmaceutical and energy sectors. By following the optimized process flow and using advanced process equipment and technology, you can ensure that you recover and purify methanol effectively and produce high quality anhydrous methanol suitable for your specific application.